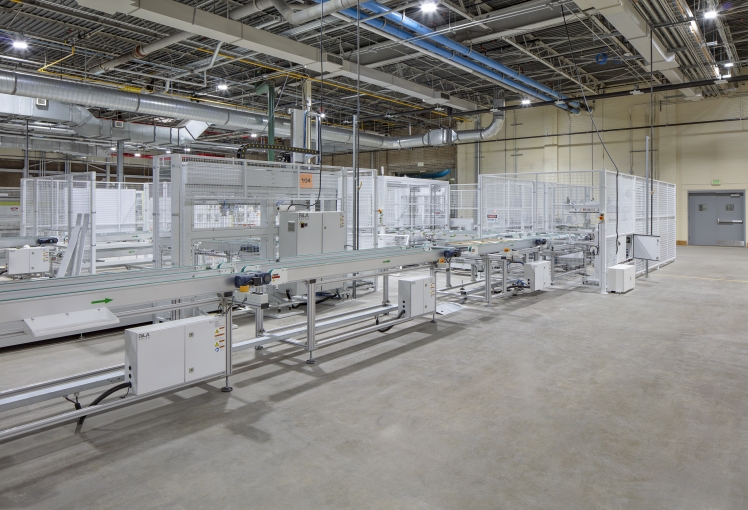
In September 2023, Bila Solar (Bila) announced it would build its North American Headquarters in Indianapolis, Indiana. Within the new facility, it would not only manufacture high efficiency, domestic solar panels but more importantly, it would introduce into the U.S. market its new patented glass-free, frameless, lightweight solar panel. The lightweight solar panel has countless uses and will be a driving factor in converting the local infrastructure into a more sustainable community, whether it be industrial, commercial, or most importantly, residential. Once all phases are complete, the new facility will create up to 250 jobs for the local community and produce 5,000 solar panels per day.
Shook was selected as the Construction Manager on this notable design-build project, in partnership with Mussett Nicholas Associates, for our reputation in the market, ability to move quickly, and industrial expertise. Beginning with an in-depth GMP process, Shook helped Bila value engineer its cost and procurement schedule to allow operations to begin as soon as possible while limiting the financial burden on the company. Just seven months later and with no prime change orders, Bila’s new facility is operational in the heart of Indianapolis.
Upon award of the project, the team needed to make adjustments to accommodate Bila's constraints. While the original cost was significant, Bila faced both time and budget limitations that prevented them from proceeding with the full project scope as initially planned. As such, Shook went through numerous iterations of the budget, scheduling, and sequencing alternatives to establish a practical GMP that would fit the tight timeline required to begin production in December 2024. This was accomplished through phasing the project, as well as value engineering to find savings. Shook dove deep into discovery to learn the true needs of the client to get the project off the ground quickly, and created a plan to add desirable, non-critical items to the facility in future phases once they were bringing in revenue. Examples include:
Shook’s approach decreased the GMP to approximately $5M, saving Bila nearly $7M as they began operations in the United States, allowing them to begin production by the end of 2024.
In order to push Bila to production as quickly as possible, the project was renovated in just seven months. Numerous challenges presented due to the age of the 60+ year old facility, material lead times, various delays in permitting and inspection, and the physical distance between some of Bila’s overseas team; however, Shook kept the critical schedule and budget a priority.
Utilizing the building’s 40-year-old switch gear to power Bila’s modern equipment was a challenge. While the building electrical feed came from a robust duel-fed substation, the installed distribution equipment was old and required some reworking. A custom-built breaker was needed to upgrade the facility; however, there was a 26-week lead time on this item that threatened to push the critical schedule. Shook worked with its subcontractors and suppliers to create an alternate plan: rerouting the power to a different transformer. Shook presented this plan to Bila and then self-performed the work. This innovative solution not only kept the project on schedule but provided $100k in savings to the client.
Additional supply chain delays on paint, carpet, aluminum postings, railings, and canopies presented, but Shook kept a close eye on these and managed them early in the project to keep the schedule. Notably, some of Bila’s equipment being sent from overseas was delayed three weeks in shipping due to a dockworkers strike at all West Coast ports of entry. Shook navigated the adversity and was able to get the equipment installed without any major schedule delays. With nearly 8,200 manhours on this project, Shook had zero safety recordables.
Shook carried the Rigging Scope Package under our contract to move all of the Owner’s production equipment. This included $5.7M of manufacturing equipment, weighing 345 metric tons (690,000 lbs). Bila’s unique equipment was shipped from overseas to Indianapolis, where Bila’s local technical team was to install it in the new U.S. Headquarters. Numerous challenges presented with assembling the foreign equipment, as it didn’t come in the correct order due to shipping delays and it had never been assembled for this particular application. Additionally, the labeling on all machines not in English, adding a further challenge in communication.
Recognizing these challenges would impact the tight schedule and potentially delay Bila’s production, Shook put together a commissioning schedule for the owner to get the equipment installed and running. This included the early production of test panels during construction close out to meet the critical schedule, which required additional support from Shook’s scheduling / project solutions team. Additionally, Shook identified numerous discrepancies translating the original design to our U.S. standards. For example, the design specified chilled water for two large pieces of equipment when it actually required ambient temperature water; the chilled water could have damaged the sensitive equipment. By careful planning and detailed reviews, Shook was able to catch these differences in verbiage before they were costly and work with the local design team of Mussett Nicholas & Associates to modify the plans.
Shook collaborated hand-in-hand with Bila throughout the project to bridge the culture gap from the team overseas to the United States, including have the owner keep a book of lessons learned for future phases of the construction projects. Some of the lessons Shook educated their team on included cultural inconsistencies, such as differences in working hours and labor, safety compliance and understanding OSHA standards, and design differences (i.e. electrical code).
Despite the many challenges, Bila’s new North American Headquarters is officially operational, and the organization looks forward to expanding its local presence in the near future.