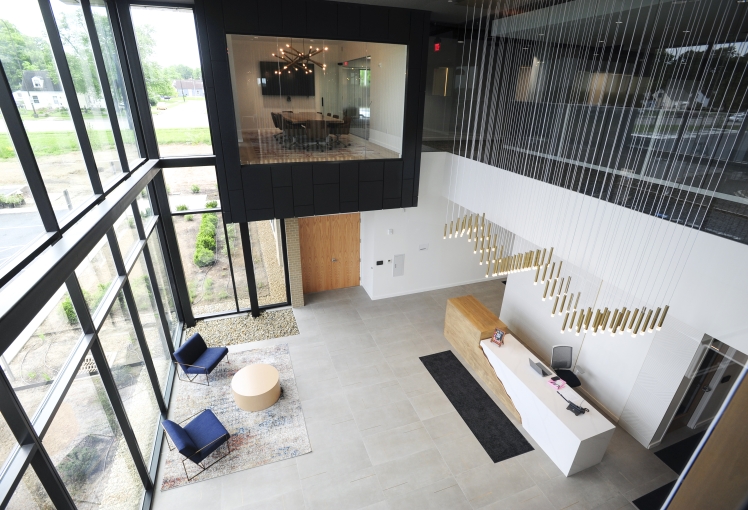
Shook served as the Construction Manager at Risk for Life Connection of Ohio’s new headquarters in Kettering, Ohio. This non-profit organization needed an expanded space to grow its life-saving work, having tripled its employees from 2020 to 2022 and increased organ donor heroes by 44% and transplants by 35% from 2020 to 2021. Their new 29,000-square-foot, two-story building replaced the 8,000-square-foot previous building that served as the headquarters for 30 years. This improved space houses the business’ main operations, including a dedicated call center, a lab area for the temporary storage and processing of tissue material (specifically kidneys), and a drive-through canopy that allows efficient delivery to the lab. As employees spend most of their days talking to those whose loved ones recently passed and facilitating organ donation, spaces for employees to decompress throughout the day and a gym were built in the facility to improve employee wellness. Additionally, a large community room is open to the public for hosting events and allows the organization to expose more people to the benefits of organ donation. With state-of-the-art technology and a new, beautiful space to call home, the facility is expected to support additional growth and, ultimately, save more lives.
Life Connection’s financing for the project included new market tax credits which contained a deadline of December 31, 2020, for the submission of Shook’s GMP. This presented a challenge as construction drawings and critical details were being developed, modified, or changed in their entirety. This regularly caused drawings to be re-issued for trade partners' pricing and subsequently, depleted the design contingency very early in the life cycle of construction. Casework, ornamental wood ceilings, balcony screen walls, door hardware, and glass folding partitions all required updated pricing and coordination with construction work already underway. Each month, Shook updated these logs and carefully explained all the changes to the budget with the CEO and Owner’s Representative. This communication effort was important to ensure transparency and accountability for changes in the work, resulting in owner-approved contingency usage.
Occurring in the heart of the COVID-19 pandemic, Shook was met with unprecedented supply chain issues on this project as many construction suppliers were unable to keep pace with ongoing demand. In order to set the stage for a successful project, our team set a realistic schedule around supply availability and identified several materials to expedite, including bar joists and roof insulation. Wasting no time, Shook locked in a production spot with a national fabricator to obtain our bar joists and substituted the specified roof insulation material for an available product. These changes allowed the new building to be under roof four months earlier than anticipated and the building envelope to be dried in before winter. By prioritizing making the building “dry-in,” we removed the impacts of inclement winter weather to the interior finishing schedule and added more control over the project sequencing. Despite the ongoing challenges with our suppliers, our crews maintained an aggressive schedule and obtained owner occupancy just 13 months after breaking ground.
Shook maintained weekly communication with the owner and project teams. Every Friday afternoon, our team sent out project updates that consisted of ongoing work, work that was started, and work that was finished. Additionally, the report included progress photos, manhours worked, schedule updates, etc. Because this project occurred during COVID-19, Shook used 360° video technology from StructionSite to provide virtual site-walk videos to the design team to prevent additional people on site and prioritize safety. This proved helpful for the AE team, as they were able to view the jobsite weekly from home and have documented progression videos throughout the project.